Introduction
This article provides an in-depth exploration of Aluminum Trim.
You'll discover key information about:
- What Aluminum Trim is
- The manufacturing process of Aluminum Trim
- Applications of Aluminum Trim
- Various types of Aluminum Trim
- And more...
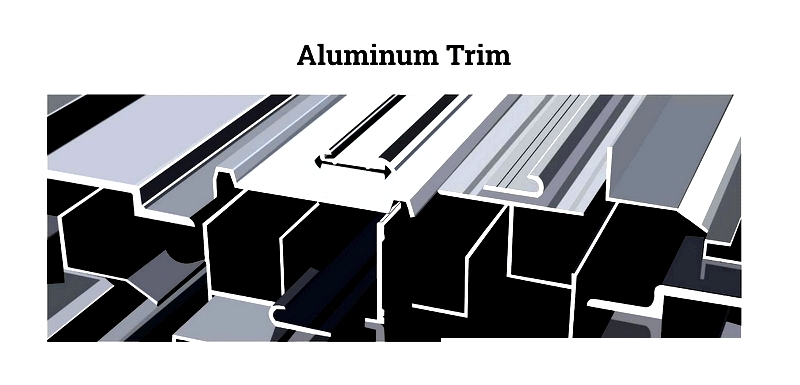
Chapter One - What is Aluminum Trim?
Aluminum trim is produced through the aluminum extrusion process, creating elongated, refined pieces ideal for architectural detailing, lighting solutions, and engineering designs. Valued for its rust resistance, corrosion protection, and lightweight properties, aluminum trim serves diverse applications.
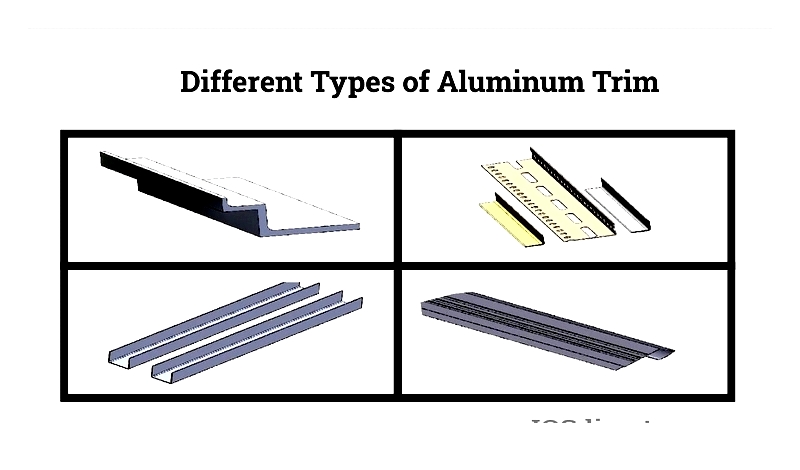
Extrusion offers a cost-effective method for manufacturing aluminum trim, delivering precise tolerances, superior dimensions, and strict adherence to design specifications.
Chapter Two - How Aluminum Trim is Made
Extrusion is the primary manufacturing method for aluminum trim, producing high-quality, durable products with excellent visual appeal. The process involves forcing malleable aluminum alloy through a die matching the desired cross-section, creating components for architecture, automotive, and construction applications.
Aluminum trim stands out for its versatility, lightweight nature, and ease of shaping. After extrusion, profiles are cut to size, inspected, finished, and packaged. Surface treatments like anodizing or powder coating may be applied for enhanced appearance and durability.
Hot Extrusion
Billet
The process begins with aluminum alloy billets, typically using 6061 and 6063 alloys for their strength and surface qualities. These materials are ideal for both structural and decorative trim applications.
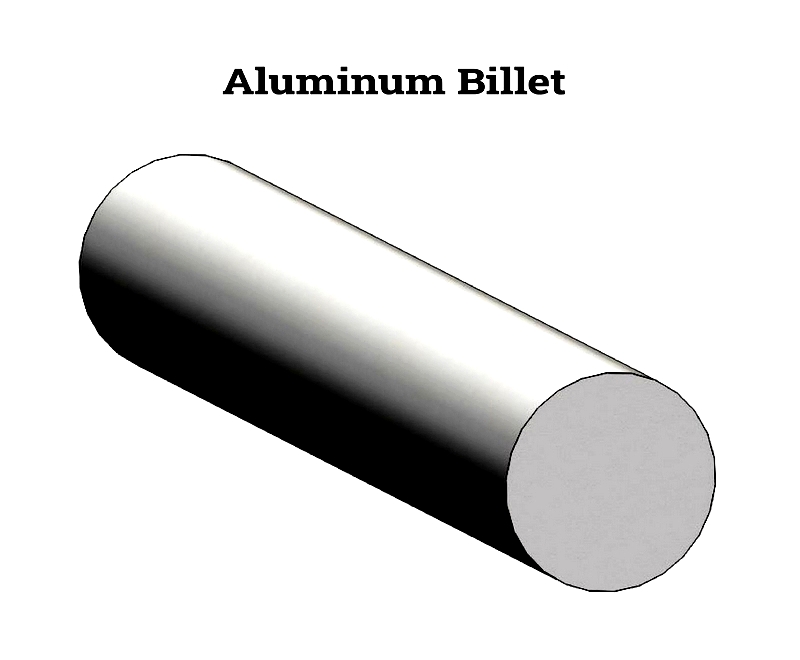
Die
Precision steel dies determine the trim's final shape. While standard profiles are available, custom dies can be created for specialized projects, ensuring proper surface area, thickness, and aesthetics.
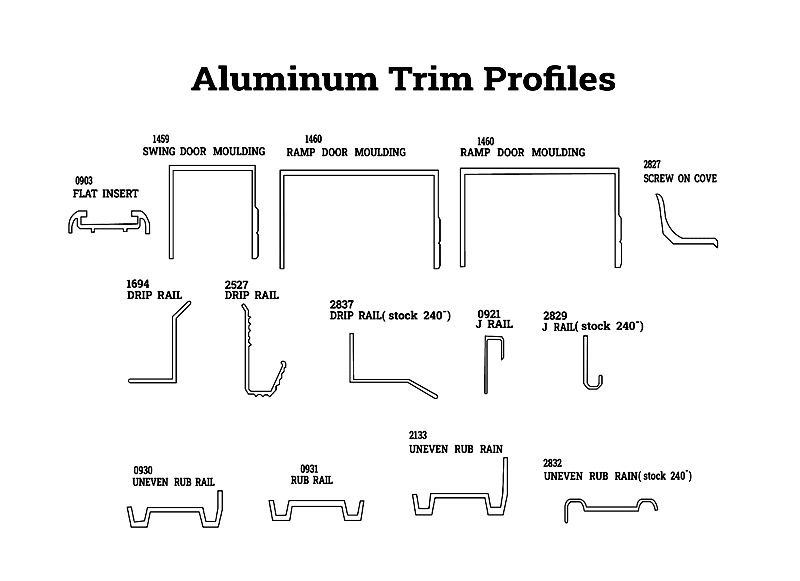
Heating
Billets are heated to approximately 800°F (426°C) to increase malleability while maintaining structural integrity, ensuring optimal material flow through the die.
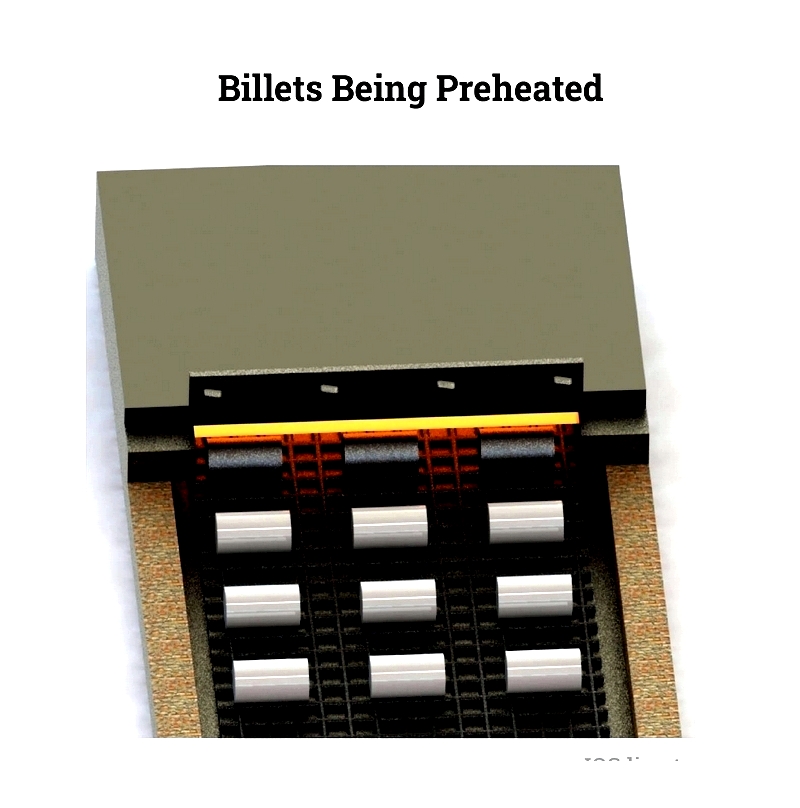
Cradle
The heated billet is secured in a cradle, maintaining alignment during pressing. A dummy block prevents material loss, ensuring consistent pressure and uniform flow.
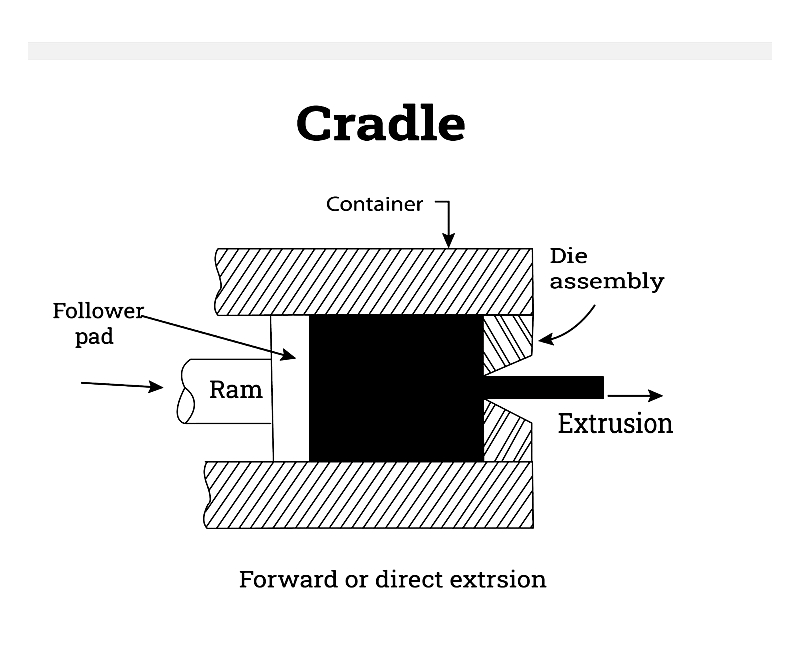
Extrusion
A hydraulic ram forces aluminum through the die, with cooling systems applied to prevent oxidation and maintain quality in the finished product.
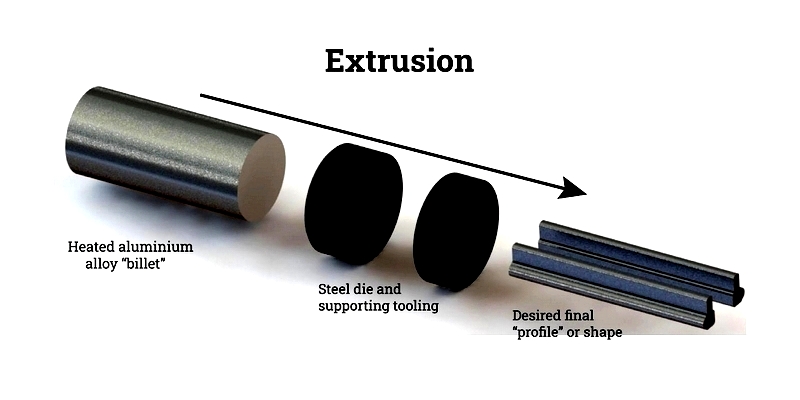
Temperature Check
Exit temperatures are monitored to ensure material consistency, with different alloys requiring specific temperature ranges for optimal results.
Runout Table
Extrusions move to a runout table where they're cooled and stabilized before being cut to length.
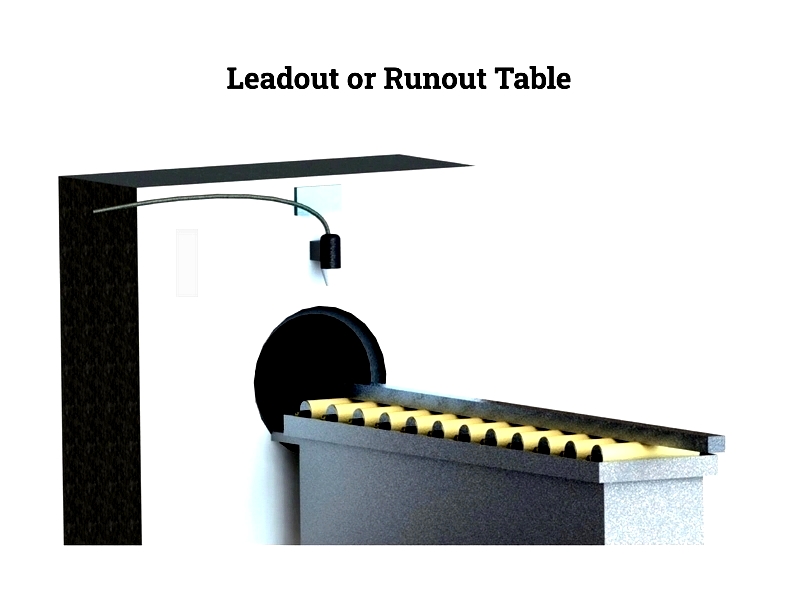
Stretching
Cooled extrusions are straightened to relieve internal stresses, improving hardness and dimensional accuracy.
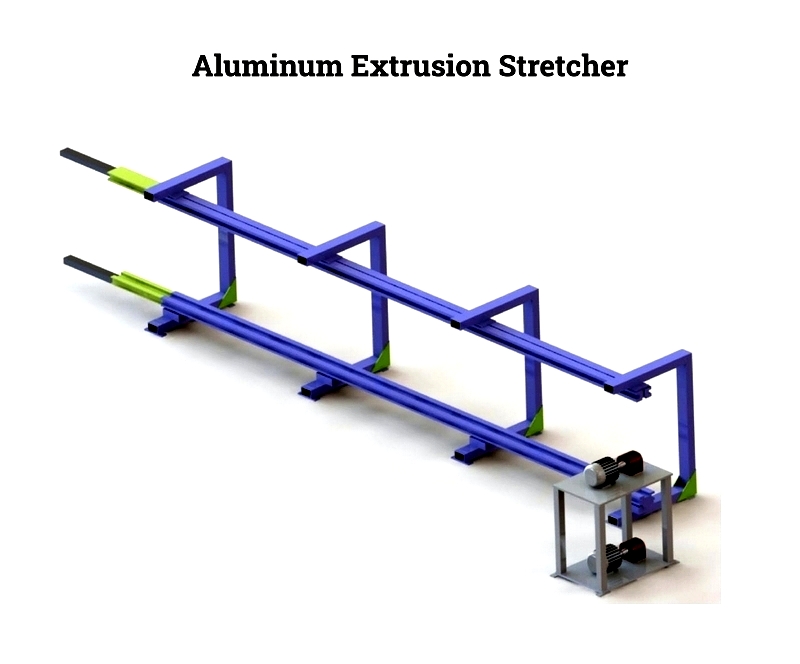
Final Cutting and Heat Treatment
Trim is cut to final lengths, with some alloys undergoing heat treatment for enhanced properties. Surface finishes may be applied for improved appearance and performance.
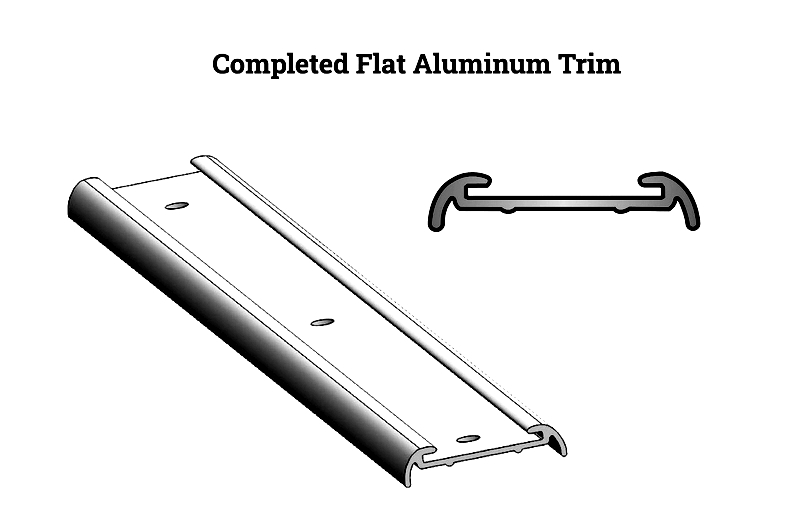
Impact Extrusion
This cold forming process uses high-velocity force to shape aluminum in a single stroke, producing strong, seamless components for packaging, automotive, and industrial uses.
Three methods are employed:
- Forward Impact Extrusion: Workpiece assumes the die's shape
- Reverse Impact Extrusion: Workpiece forms around the punch
- Combination Impact Extrusion: Uses both die and punch for complex shapes
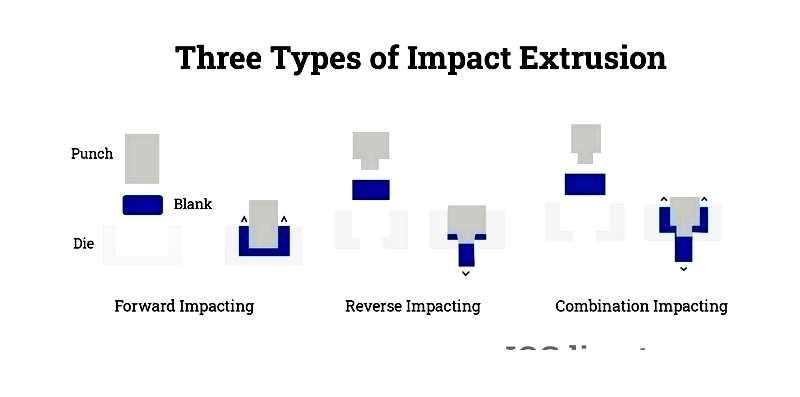
While efficient for symmetrical shapes, the process has limitations for complex profiles, making traditional extrusion preferable in some cases.
Choosing the Right Aluminum Trim
Key considerations include:
- Alloy Selection: Choose based on strength, corrosion resistance, and workability needs
- Profile Design: Balance custom requirements with cost efficiency
- Surface Finishing: Select treatments for both protection and aesthetics
- Value-Added Services: Consider machining and assembly options
- Customization: Verify minimum order quantities and tooling costs
Consulting with experienced manufacturers ensures trim meets all specifications for performance and appearance.
Chapter Three - Leading Aluminum Trim Machines
Specialized equipment is essential for quality aluminum trim production. Below are five prominent brands and their flagship models:
Brand: Mitten Inc.
Model: Mitten TrimFormer
Features precision bending and shaping capabilities with adjustable tooling for custom profiles, suitable for high-volume production.
Brand: Gentek Building Products
Model: Gentek TrimMaster
Specializes in high-speed cutting and bending for window and door trim, with minimal downtime between operations.
Brand: Rollex Corporation
Model: Rollex TrimFormer
Utilizes roll-forming technology for consistent exterior trim production, with digital measurement for accuracy.
Brand: Spectra metal Sales
Model: Spectra TrimRollformer
Automated roll forming machine capable of producing various trim profiles with efficient material handling.
Brand: Quality Aluminum Products
Model: QAP TrimMaster
Robust machine with advanced safety features and versatile tooling for diverse trim applications.
When selecting equipment, consider capacity, automation, profile compatibility, and support services. Key features to look for include:
- Precision cutting and bending capabilities
- Quick-change tooling options
- Automated controls for consistent quality
- Durable construction for continuous operation
- Integration with material handling systems
Choosing the right machine enhances production efficiency and product quality for aluminum trim manufacturers.