Introduction
This article offers a comprehensive overview of bevel gears, covering the following aspects:
- What is a Bevel Gear?
- Bevel Gear Efficiency
- Types of Bevel Gears
- Geometry and Terminology
- Manufacturing Methods
- Bevel Gear Applications
- Additional Information
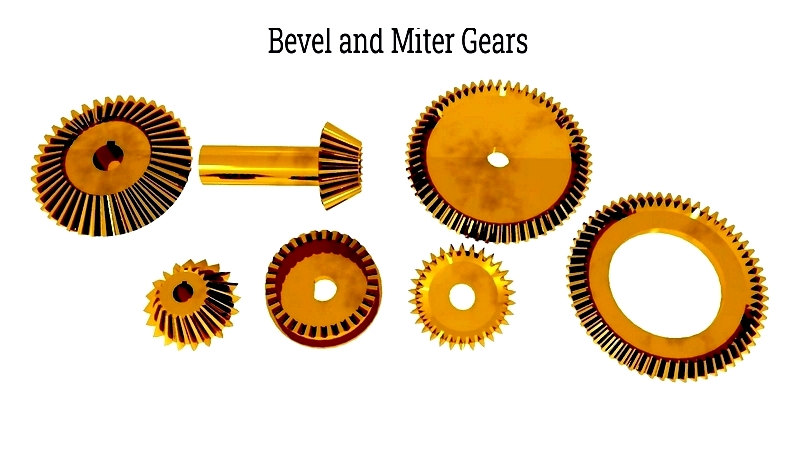
Chapter 1: Understanding Bevel Gears
Bevel gears are toothed mechanical components that transfer power between intersecting shafts, typically at right angles. They change the rotation axis and can modify torque levels while inversely affecting angular velocity.
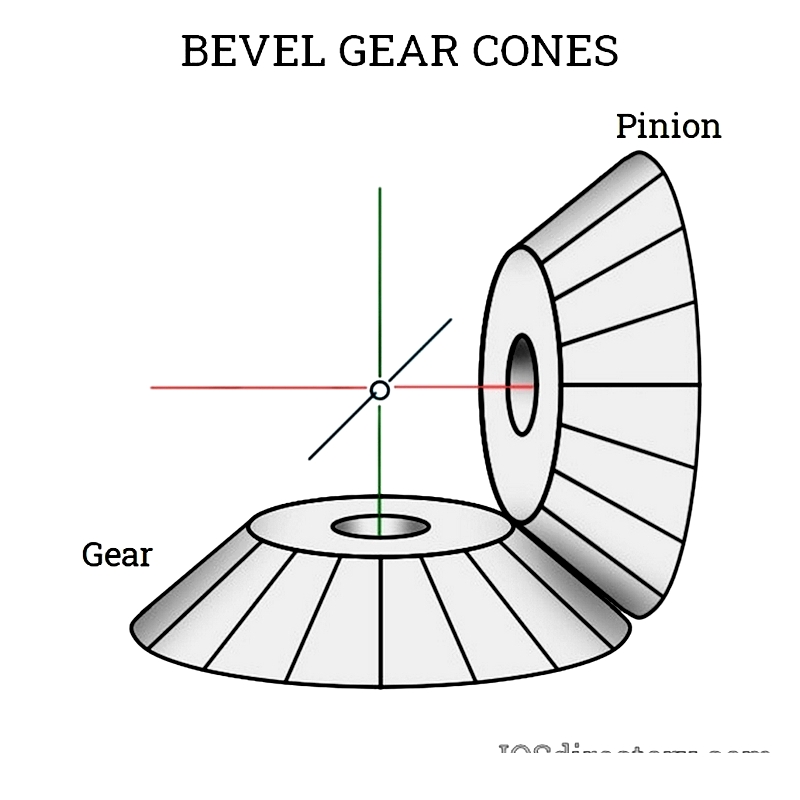
Structurally resembling a truncated cone, bevel gears feature teeth along their tapered surfaces that mesh with other gears. The power-transmitting gear is called the driver gear, while the receiving gear is the driven gear. These gears usually have different tooth counts to create mechanical advantage. The gear ratio compares the driven gear's teeth to the driver gear's teeth, with mechanical advantage being the output-to-input torque ratio, as shown:
Mechanical advantage depends on torque values (τb and τa), gear radii (rb and ra), and tooth counts (Nb and Na). The equation demonstrates that increasing driven gear teeth produces greater output torque.
Conversely, higher mechanical advantage reduces the driven gear's output speed, as expressed by:
Here, ωa and ωb represent the angular velocities of driver and driven gears respectively. A 10:1 ratio is optimal for torque multiplication, while 1:5 suits speed enhancement.
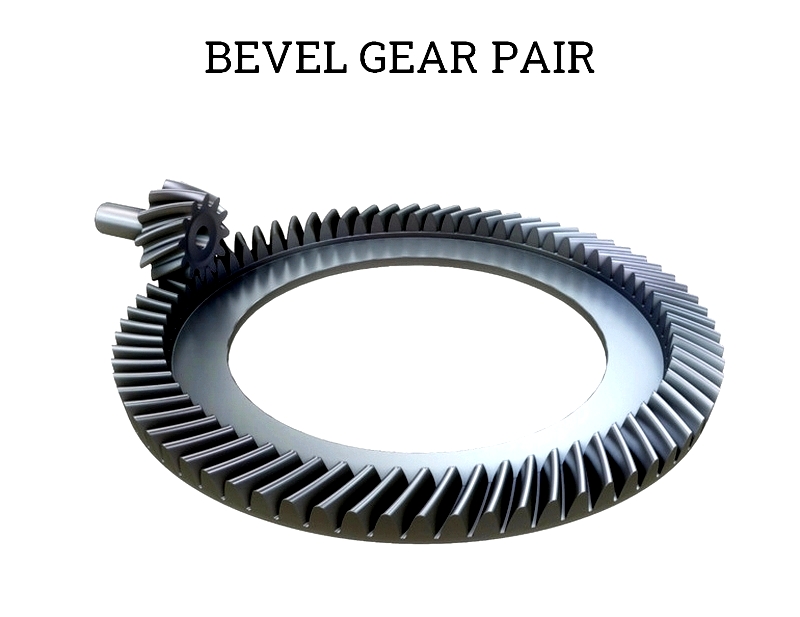
Bevel gears must be used as matched pairs and not interchanged. Unlike spur gears that mainly handle radial loads, bevel gears are designed to transmit both thrust and radial loads. Proper assembly ensures optimal performance.
Chapter 2: Bevel Gear Efficiency
Efficiency in mechanical power transmission refers to the ratio of output to input power. While mechanical advantage focuses on force amplification with speed trade-offs, efficiency measures power transfer effectiveness with minimal losses. In bevel gear systems, power loss primarily occurs through tooth friction, sliding action, and bearing/housing forces. Proper lubrication and precision engineering minimize these losses, enhancing efficiency and longevity. Understanding efficiency is crucial when selecting gears for automotive, industrial, robotic, and heavy equipment applications where performance and energy conservation matter.
Bevel gears—including straight, spiral, zerol, and hypoid types—transmit power between intersecting shafts. Their efficiency varies with geometry, application, load capacity, and alignment precision. The table below compares efficiency ranges and bearing loads, showing bevel gears' superiority over alternatives like worm gears.
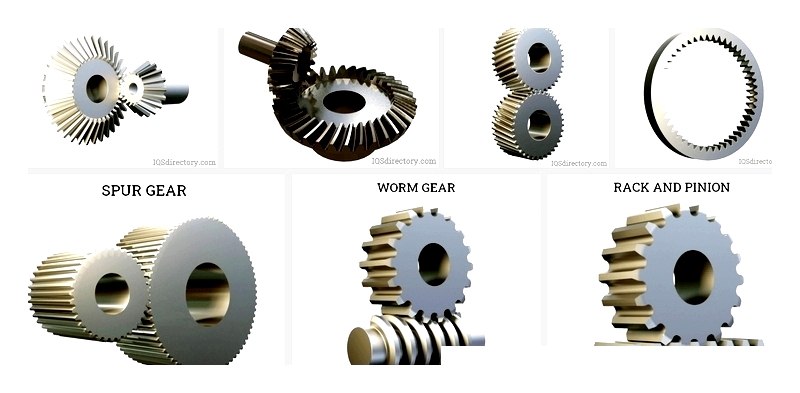
Efficiency Factors
Key factors affecting bevel gear efficiency include:
- Tooth design and finish: Precision-machined teeth minimize friction and heat generation.
- Lubrication quality: Specialty oils reduce wear and maintain efficiency.
- Alignment precision: Proper installation prevents premature failure.
- Operating conditions: Excessive speed or load can decrease efficiency.
When selecting bevel gears, consider efficiency along with torque capacity, gear ratio, noise levels, and application suitability. Consulting with specialized manufacturers helps identify optimal materials (like alloy steel) and custom solutions.
For sourcing high-efficiency bevel gears, evaluate suppliers based on quality, certifications (ISO 9001), customization options, and support services to ensure reliable power transmission solutions.