Introduction
This article provides an in-depth exploration of cold heading and cold forming processes.
Key topics covered include:
- Principles of Cold Heading
- Various Cold Heading and Cold Forming Processes
- Applications and Benefits of Cold Forming
- Additional relevant information
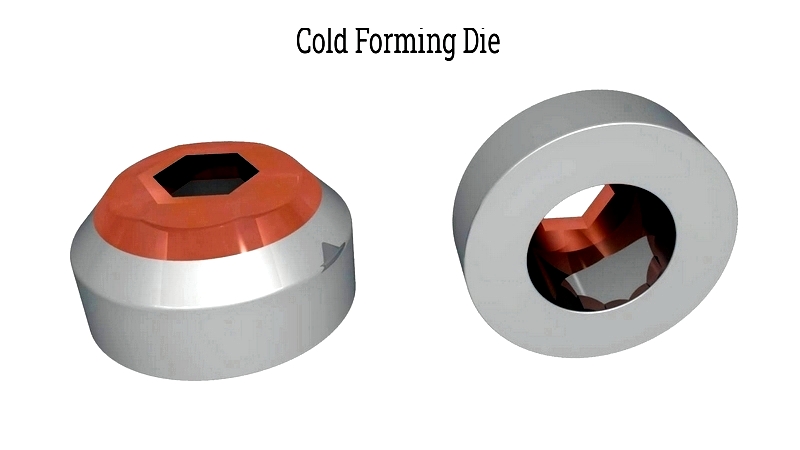
Chapter 1: Understanding the Basics of Cold Forming
This chapter examines the fundamentals of cold forming, including material selection and tooling methods used in production.
Understanding Cold Heading
Cold heading, or cold forming, shapes metal wire at room temperature using high-speed hammers, dies, and punches.
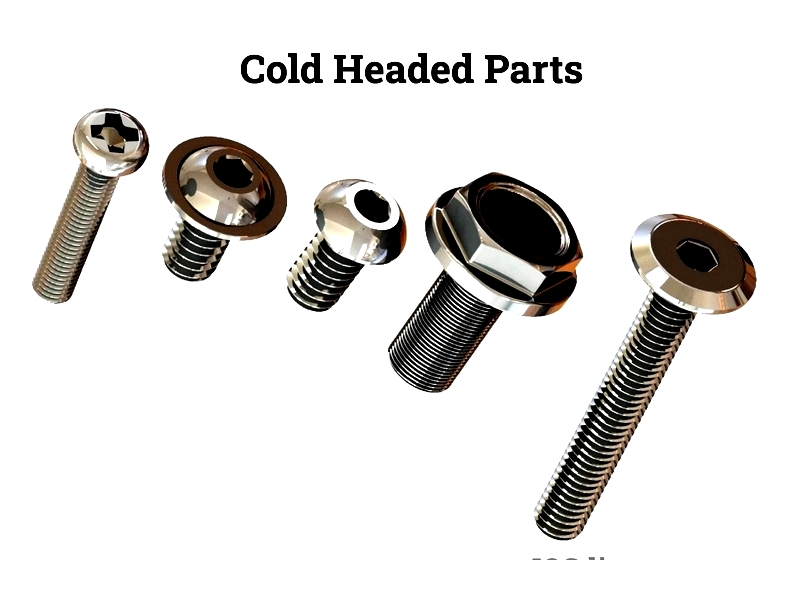
The process starts by cutting wire slugs, which are then formed through successive hammering and die operations that exceed the metal's yield strength.
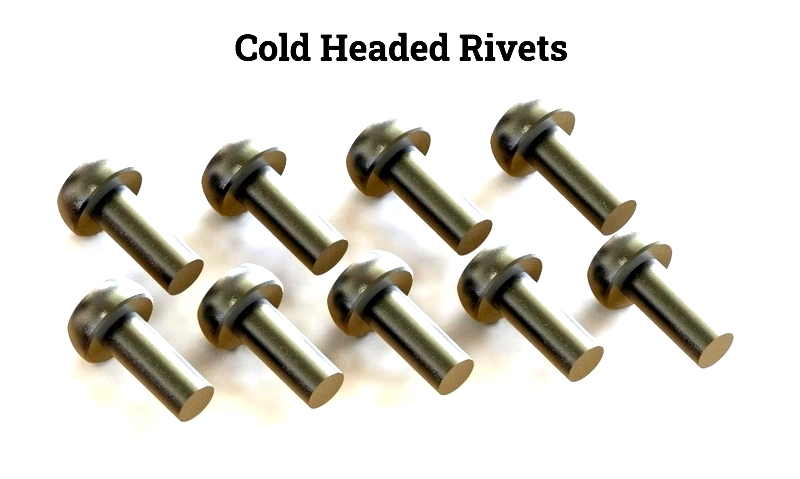
This forging technique produces threaded fittings and fasteners through operations like rolling, piercing, and trimming without heat application.
Originally for simple fasteners, modern cold heading now handles complex components in tough alloys through automated, multi-station processes.
Tools and Materials in Cold Forming
Specialized equipment cuts and measures wire coils, with variations among manufacturers' feeding mechanisms.
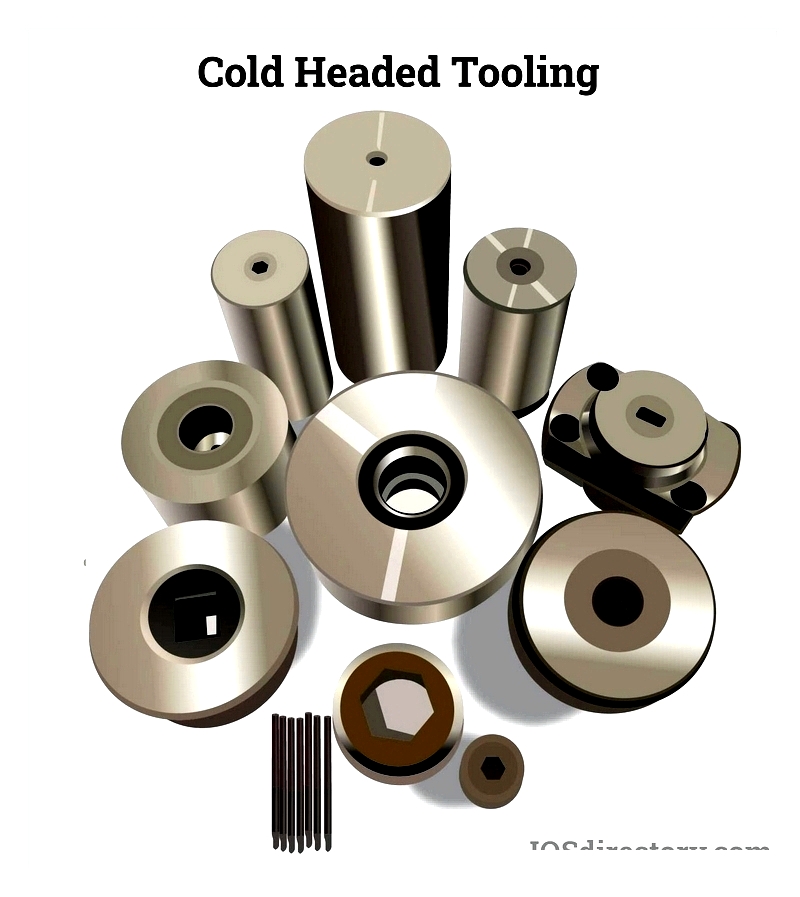
Cold Forming Dies
Stationary dies withstand high pressures through segmented construction within reinforced casings.
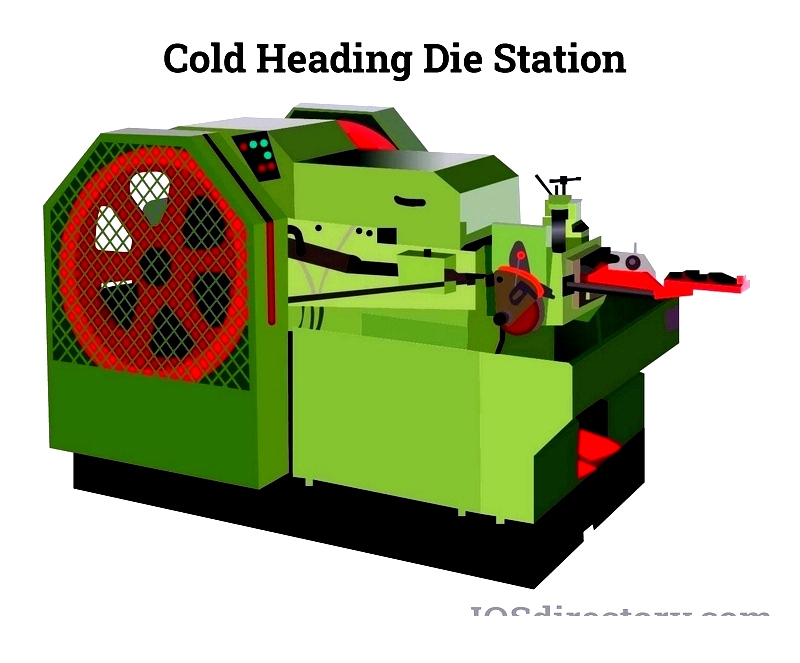
Proper die support prevents premature failure, with knock-out pins ensuring part release after forming.
Cold Forming Punches
Movable punches shape screw heads through multiple impacts while supporting extrusion operations.
Cold Forming Transfer
Precision transfer systems move parts between dies in multi-station headers, requiring exact timing.
Cold Heading Machines and Processes
Reciprocating rams drive hammers into dies to transform metal blanks into precise shapes.
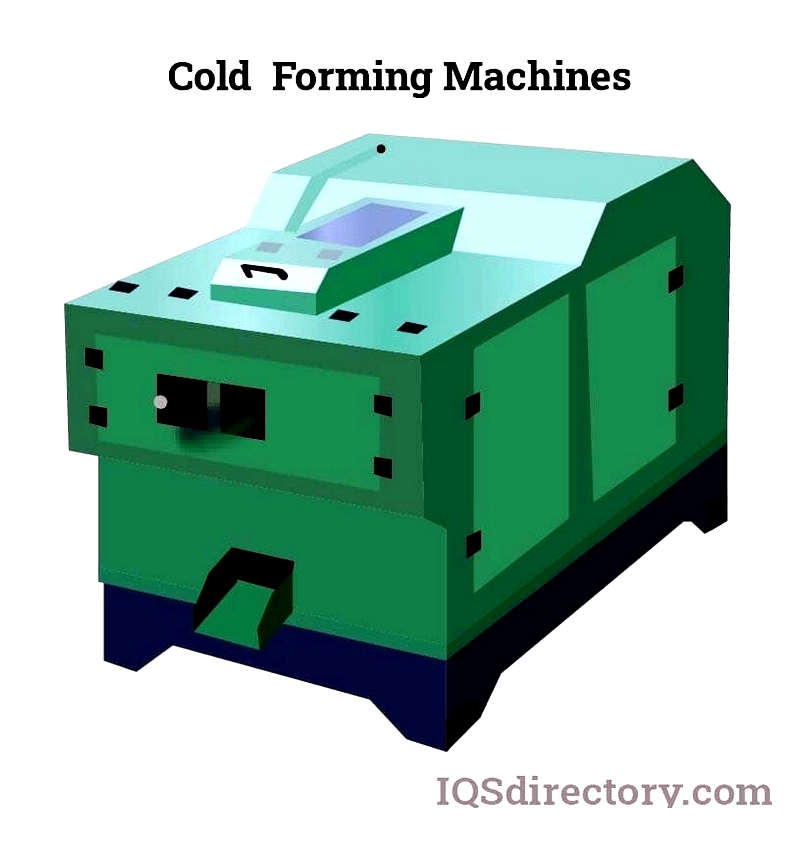
Modern machines feature improved gear systems for quieter operation and higher productivity.
The Art of Cold Heading
Automated equipment converts wire into complex components at rates up to 400 parts per minute with minimal waste.
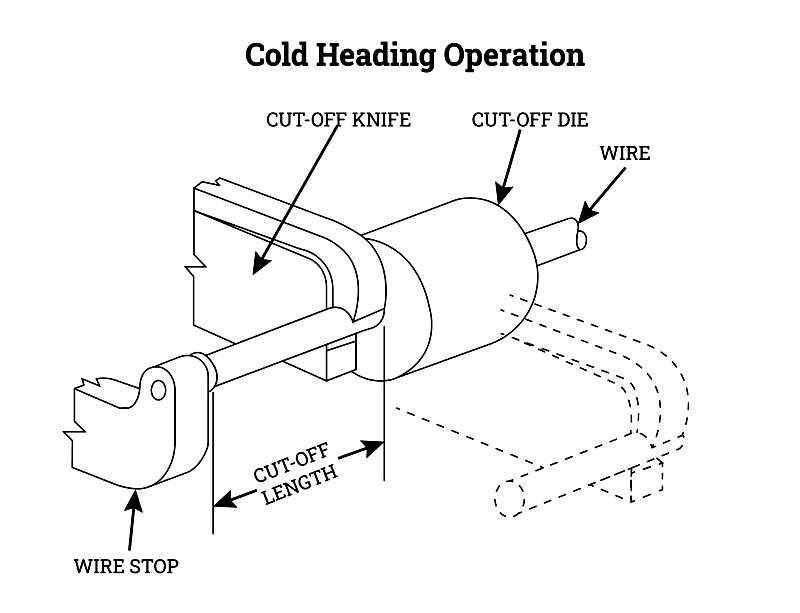
Innovations in Cold Forming Machinery
Recent advancements include multi-die configurations and CNC controls for efficient production of diverse parts.
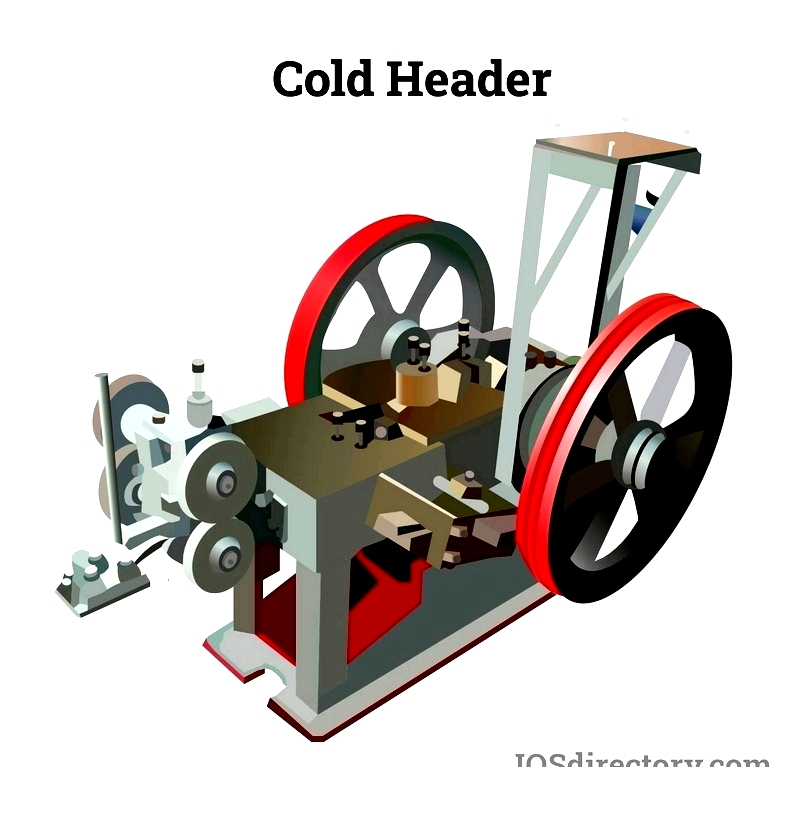
Improved metallurgy enables forming stronger materials while extending tool life through specialized alloys.
Chapter 2: Types of Cold Heading Processes
Types of Cold Heading Equipment
Cold heading systems fall into two main categories:
- Part formers
- Cold headers
Both use horizontal rams to shape metal at room temperature, ranging from single-die to seven-die configurations.
Types of Cold Heading Processes
Cold heading primarily involves upsetting and extrusion techniques for metal forming.
Cold Heading Upsetting
This process forms fastener heads by consolidating material through controlled deformation.
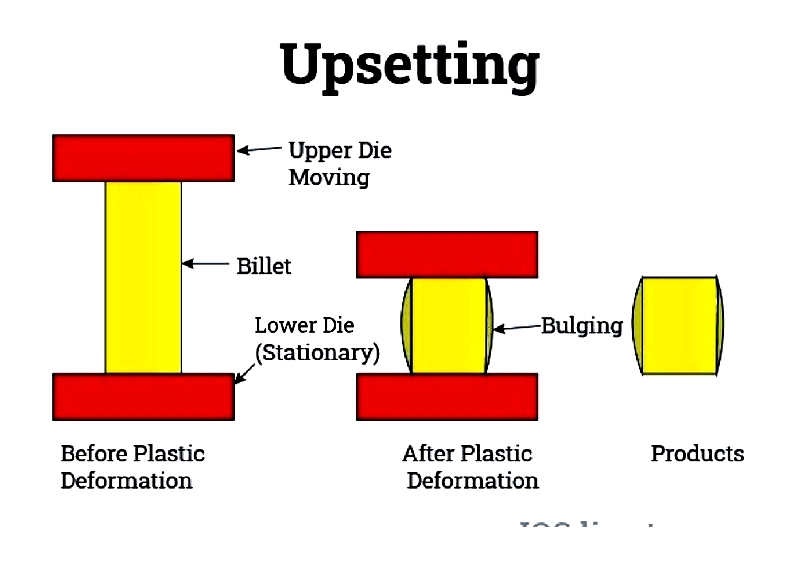
Multiple die stations enable complex head geometries while maintaining material integrity.
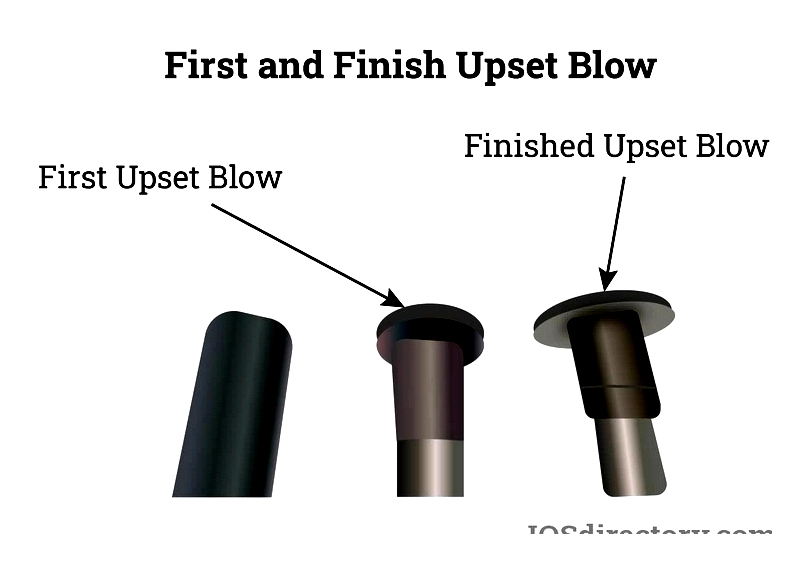
Cold Heading Extrusion
Extrusion techniques include:
- Forward extrusion (trapped and open)
- Reverse extrusion

Open Extrusion
Produces long, slender components with greater material flow but higher force requirements.
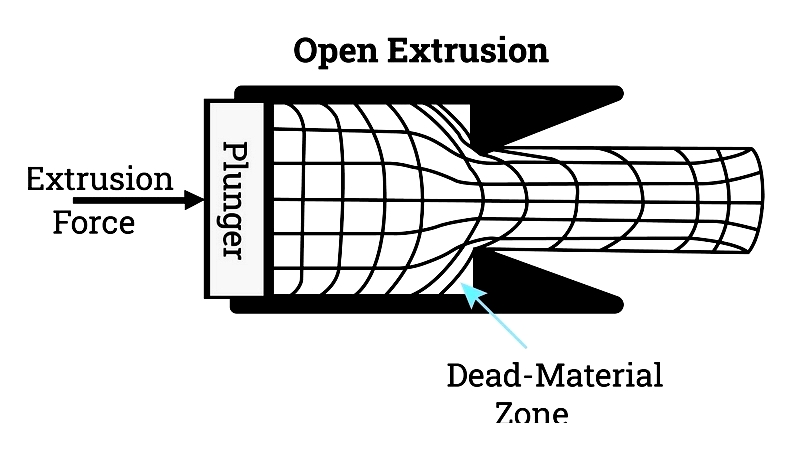
Trapped Extrusion
Enables complex geometries through fully contained forming with greater diameter reduction.
Reverse Extrusion
Creates hollow features like internal recesses and drive sockets in fasteners.
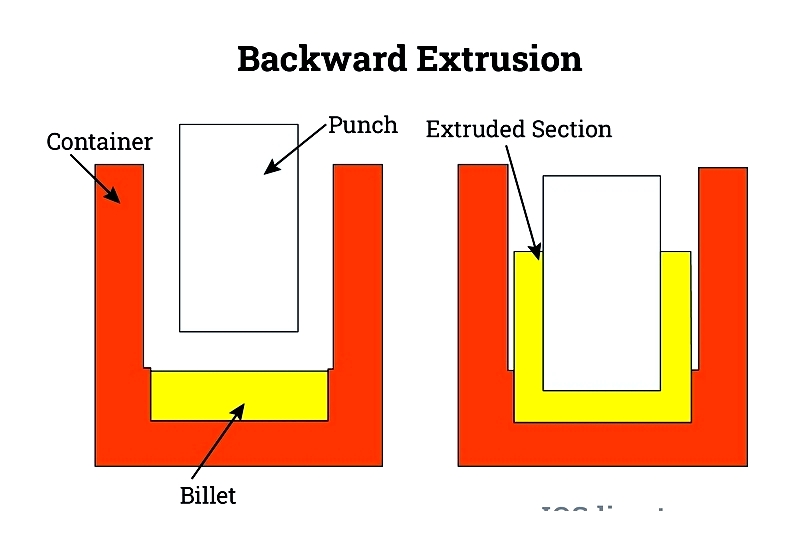
Chapter 3: Applications and Advantages of Cold Heading
This chapter examines cold heading's industrial uses and benefits.
Applications of Cold Heading
The process efficiently produces high-quality fasteners from specialized cold heading steels and alloys.
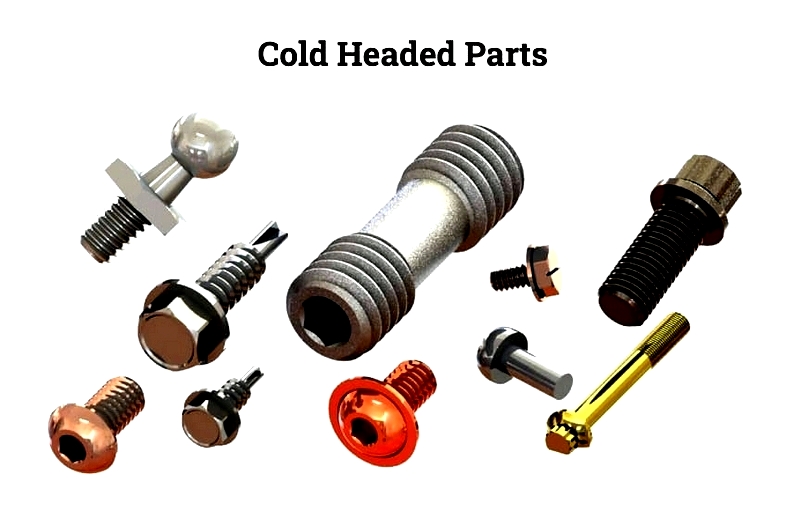
Advantages of Cold Forming
Key benefits include:
Fast Production
High-speed operations yield up to 100 parts per minute with consistent quality.
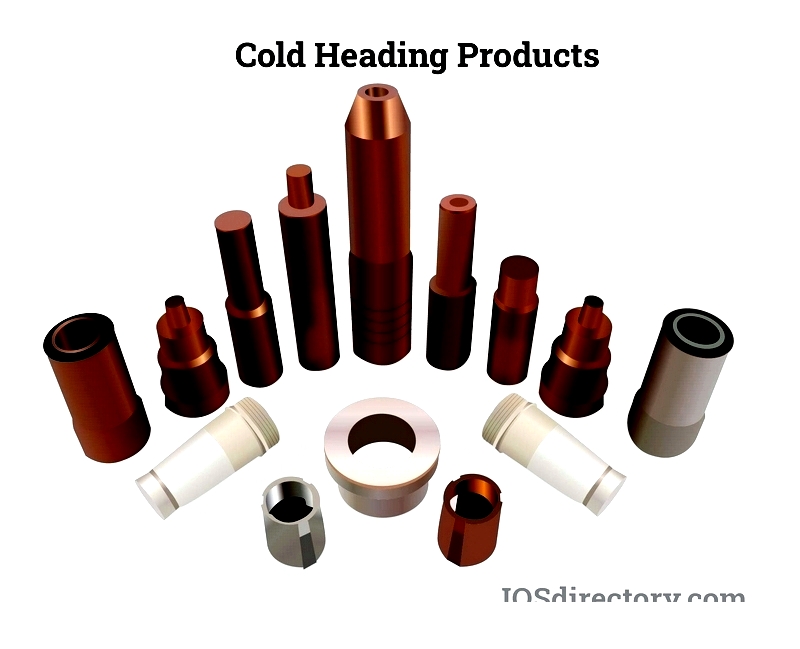
Added Strength
Maintains material grain structure for enhanced durability.
Reduced Energy Consumption
Eliminates heating requirements found in hot forging processes.
Drawbacks of Cold Heading
Limitations include:
Size Limitations
Practical constraints exist for extremely large fastener production.
Material Limitation
Not all metals are equally suitable for cold forming processes.
Conclusion
Cold heading has significantly advanced manufacturing technology, offering efficient production of high-quality components when properly applied.