Introduction
This comprehensive guide covers all aspects of permanent mold casting.
You'll discover:
- The fundamentals of Permanent Mold Castings
- How the Permanent Mold Casting Process operates
- Common products manufactured through Permanent Mold Casting
- Practical applications of Permanent Mold Castings
- Additional valuable insights
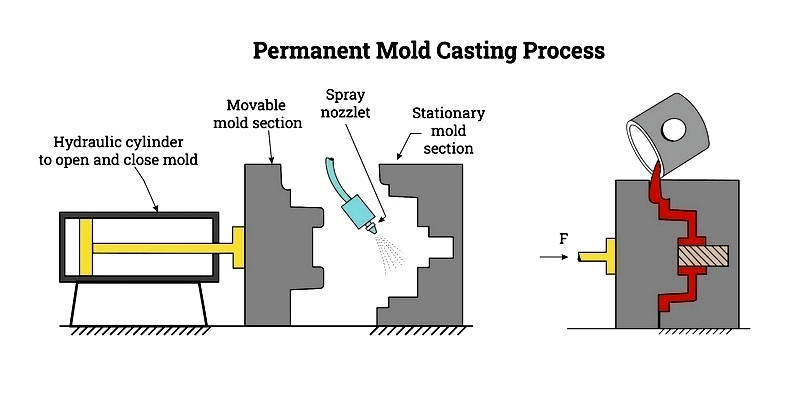
Chapter 1: What Are Permanent Mold Castings?
Permanent mold casting utilizes durable, reusable molds to manufacture metal components from molten materials. Typically constructed from steel or cast iron, these molds endure repeated use while producing thousands of precise parts. Although frequently employed for aluminum, copper, and magnesium alloys, this method works with any metal that can be melted.
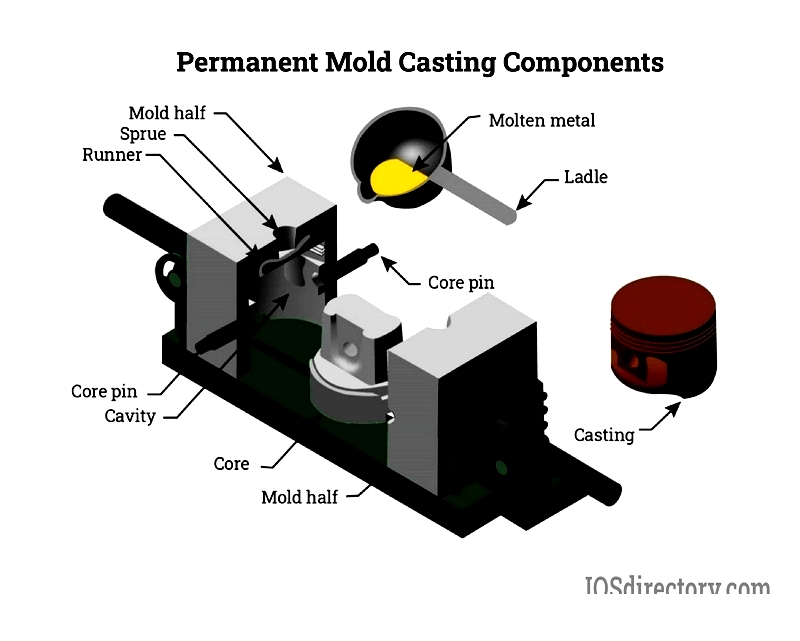
This casting method's popularity stems from its ability to deliver tight tolerances, smooth finishes, and excellent mechanical properties. Unlike sand casting or lost wax casting that use disposable molds, permanent mold casting employs reusable molds. During solidification, the mold's solid surface rapidly cools the metal, creating a finer grain structure and reducing porosity in the final product.
Chapter 2: What is the Permanent Mold Casting Process?
The molds in permanent mold casting are critical for achieving precise final product tolerances. Each process step must be carefully executed and monitored to ensure the result meets design specifications, dimensional standards, and tight tolerances. These quality measures are essential in industrial manufacturing for producing high-quality metal components that satisfy customer needs and application requirements.
Permanent mold casting encompasses various metal casting techniques that use durable molds for mass production. Unlike expendable mold processes like sand casting, permanent mold casting employs sturdy molds made from high-strength materials that withstand repeated heating and cooling cycles. While methods vary, they all involve introducing molten metal into preheated, coated mold cavities. The specific pouring technique—whether gravity die casting, low-pressure permanent mold casting, vacuum die casting, or slush casting—depends on part complexity, required surface finish, production volume, and mechanical properties. Each method offers unique advantages for industries like automotive, aerospace, electronics, and industrial manufacturing, addressing different needs such as precision, durability, and cost-effectiveness.
Creating the Mold
Permanent mold casting requires engineering durable molds from materials like tool steel, cast iron, graphite, or copper-based alloys. These materials withstand repeated thermal cycling and mechanical stresses from high-temperature molten metals. Depending on part complexity, molds may include multiple sections with features like cores, inserts, and venting systems for optimal metal flow and gas evacuation.
The mold production process begins with designing an accurate pattern for the finished component, incorporating gating systems, runners, channels, and sprues to guide molten metal. Since molds typically split into multiple sections, these features must be carefully positioned to ensure even distribution, complete filling, and minimal defects. Advanced CAD software often assists in mold design, simulating flow and solidification to optimize quality and consistency.
The mold cavity precisely replicates the object's negative form, ensuring each casting matches the original design. Permanent molds offer significant advantages over disposable molds, including better dimensional accuracy, reduced porosity, enhanced mechanical properties, and consistent surface finishes. The solid structure of steel or iron molds also helps control wall thickness and heat transfer, improving casting durability and structural integrity.
Mold manufacturing time varies based on complexity, size, and production needs. The tooling process involves collaboration between engineers, foundry personnel, and sometimes customers. Detailed design reviews precede actual machining, which may take one week to over a month. However, with proper maintenance, permanent molds can produce thousands to tens of thousands of parts, making them cost-effective for high-volume production. Key performance factors include mold material, operating temperature, casting alloy type, and cooling methods.
Guide pins, alignment pins, or locating pins ensure precise mold closure and alignment, preventing flash and maintaining dimensional tolerances. These features are crucial for high-quality parts and support automated or semi-automated casting operations.
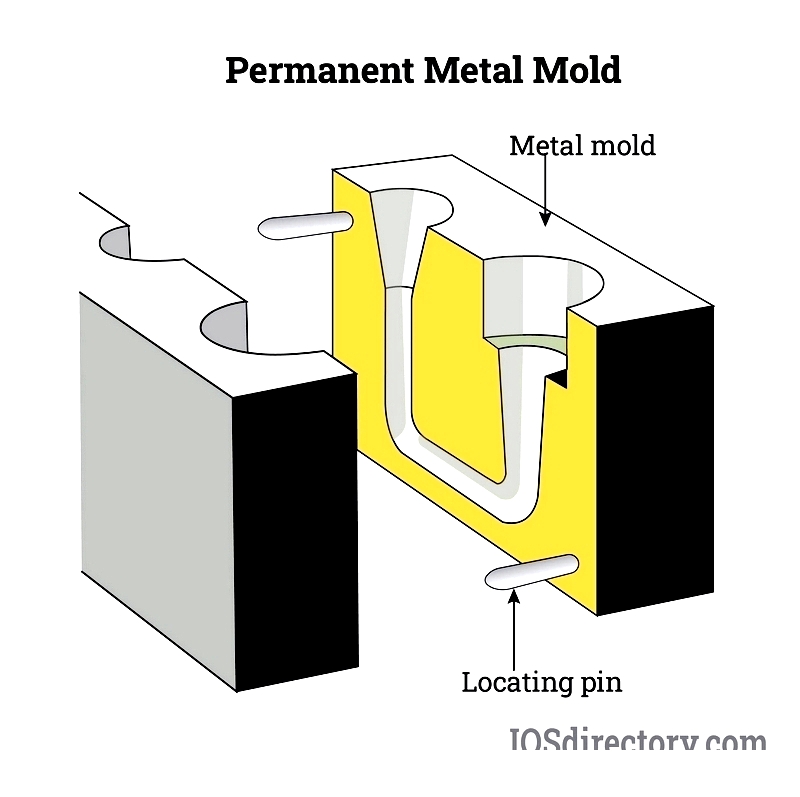
Heating the Mold
After use, casting companies typically clean and store molds under controlled conditions for future projects. Each new production cycle begins by preheating the mold to a temperature suitable for the casting alloy—usually between 150°C and 300°C (302°F to 572°F). Preheating ensures even metal distribution, prevents thermal shock, and promotes uniform cooling. Proper preheating helps avoid defects like misruns or cold shuts.
Before pouring, mold halves receive a heat-resistant, non-stick coating—often ceramic or graphite-based—that withstands thermal cycles and facilitates part removal. These coatings improve surface finishes and extend mold life. Specialized preheating stations or ovens ensure precise temperature control, with some foundries incorporating advanced sensors, robotic handling, and automated monitoring for optimal results.
Choosing the metal
Permanent mold casting works with various non-ferrous and ferrous metal alloys, though aluminum, magnesium, copper, and zinc-based alloys are most common due to their lower melting points and excellent casting properties. The selected alloy influences processing parameters—mold temperature, molten metal temperature, pouring rate, applied pressure, and cooling rate—as well as final properties like tensile strength, ductility, corrosion resistance, and machinability. Part complexity and function also determine alloy selection, as some alloys offer better fluidity, weldability, or support for intricate shapes. Collaboration between design engineers and foundry experts ensures optimal process, alloy, and post-casting treatment combinations for superior part performance.