Introduction
This article provides an in-depth exploration of forging.
You will learn about various topics, including:
- A brief history of forging
- Hot forging and its working principles
- Key considerations when selecting hot forging
- The advantages of cold forging or forming
- important factors for choosing cold forging

Forging: A Historical Overview
Forging is an ancient metalworking technique with two main variants: hot and cold forging. While hot forging has been practiced for centuries, cold forging gained prominence during the 19th-century Industrial Revolution. Both methods share the common goal of reshaping metal, with the choice between hot, cold, or warm forging depending on the metal type and desired product specifications.
Understanding Hot Forging
Hot forging involves heating metal significantly above its recrystallization temperature. This temperature varies by material: steel requires up to 1150°C, aluminum alloys need 360°C to 520°C, and copper alloys range between 700°C and 800°C. Maintaining temperatures above this threshold is critical, as dropping below can cause crystal formation that strain-hardens the material, making it difficult to work.
Environmental factors affect hot forging, as atmospheric exposure may cause oxidation. Solutions include using controlled environments or isothermal forging, similar to vacuum conditions.
Hot forging significantly improves metal strength. The process enhances ductility, allowing extensive deformation that increases tensile stress resistance. It also optimizes the metal's grain structure, improving the final product's strength and structural integrity.
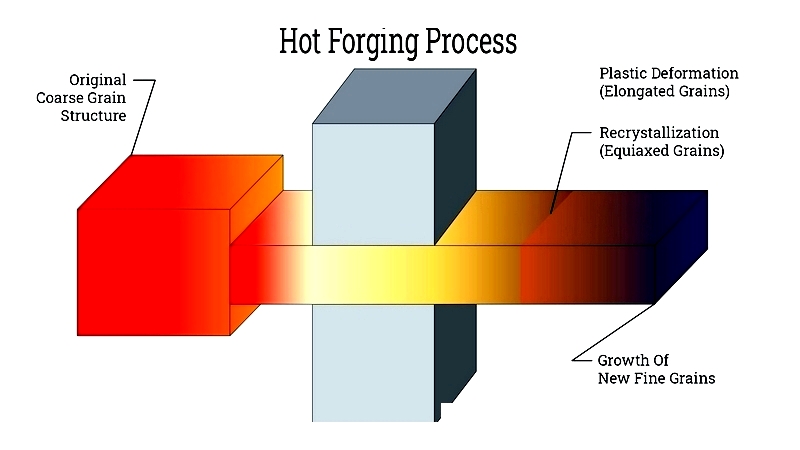
Considerations for Hot Forging
Hot forging excels at producing complex, high-precision components, particularly for highly formable metals. The process increases strength and durability while enabling custom part production. Additionally, hot-forged parts feature superior surface finishes compatible with various polishing techniques.
The benefits of hot forging include efficient single-part production, though with slightly lower precision than other methods. While it may cause surface scaling, it reduces metal stress by minimizing work hardening temperatures. The process also promotes uniform grain structure, enhances ductility, and corrects material inconsistencies.
Drawbacks of Hot Forging
Despite its advantages, hot forging has some limitations. Cooling can cause warping and brittleness, and certain metals are unsuitable due to potential grain structure variations and tolerance issues.
While hot forging has these constraints, it remains invaluable for aerospace applications. The process improves metal malleability, enabling the creation of complex shapes and detailed designs required in this industry.